Case Study
LaserStar Technologies
RIM as a Replacement for Sheet Metal
When LaserStar Technologies developed their original 7000 Series LaserStar Workstation, and the iWeld Professional Series, Reaction Injection Molding was chosen as the perfect replacement tor sheet metal because of its exceptional design freedom, aesthetic appeal and improved ergonomics.
LaserStar Technologies develops equipment that offers an alternative to soldering and micro‐plasma welding for precious metal jewelry production, fabrication and repair of dental prosthetics, and microassembly of medical devices and electronic components. The company’s laser welding workstations eliminate the need for solder by using a sharp, focused laser beam to fuse together any two metal parts. When developing the workstations, they turned to one of the country’s leading providers of RIM Technology and Exothermic Molding, Inc. to provide improved economics, ergonomics and more aesthetic appeal.
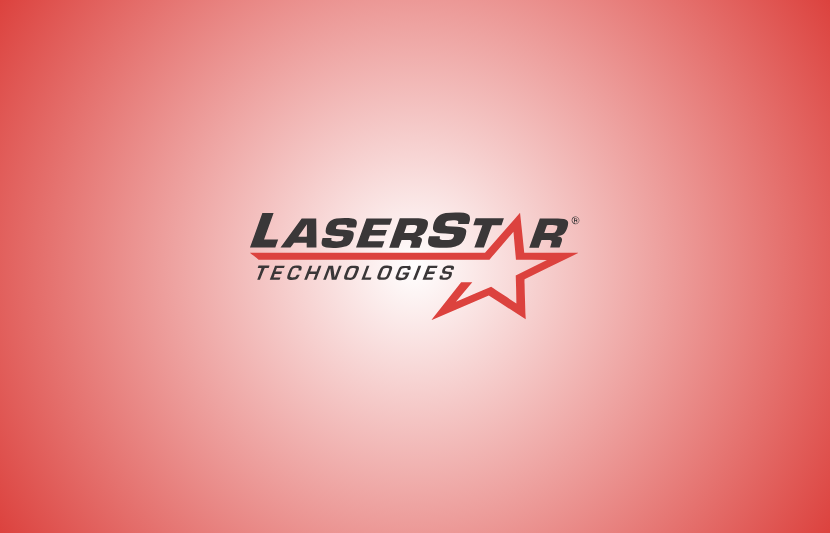
Reaction injection Molding was selected to replace sheet metal because of the design freedom it offers and the stylish look it is capable of producing. According to Product Designer Justin Sirotin, originally of Item New Product Development, and now, OCTO Product Design, the RIM process provided an ideal platform to take the products styling to the next level. The designers wanted a more appealing, softer appearance with curved surfaces and flowing lines. Aesthetics sheet metal could not achieve.
The superior finishing capabilities of Exothermic Molding also added appeal to the work station housing. The RIM parts are beautifully finished an array of colors, offering buyers a choice to best suit surrounding décor.
A functional purpose, however, made RIM the ideal choice. Because of curved and contoured shapes, design engineers were able to significantly improve the ergonomics of the work stations. Development incorporated large ribs under the surface of such parts as the access door for reinforcement, as well as molded‐in bosses and inserts for assembling the parts.
Exothermic produced four low‐cost, machined, aluminum molds to create the five parts used on the 7000 Series workstation façade ‐ a left cuff, a right cuff, a bezel, door assembly and a foot rest cover at the base. When the company began producing its iWeld Professional Series, two molds were tooled and are now used to produce three parts. The molds were fashioned directly from the CAD files supplied by LasterStar, and machined at Exothermic Molding.
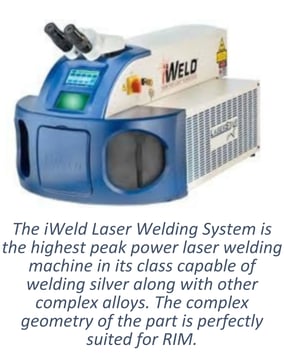
The Benefits Of Reaction Injection Molding
-
Large, sculpted parts can be molded economically.
-
Variable thickness walls within the same mold allow for greater design freedom. Wall thickness may range from .125 to 1.125 inches.
-
Closed molds produce accurately molded and structurally strong parts.
-
Lower tooling cost and shorter tooling lead time.
-
A wide variety of material properties including UL94VO.
-
Electronic components, metal parts, glass, and other materials are easily encapsulated.
-
RIM parts are lower cost than the same parts made from metal or fiberglass.
-
Compared to fiberglass, RIM parts have improved repeatability.
-
Composites - RIM parts can be reinforced with many materials.
Exothermic Molding Capabilities
-
CAD Engineering Review
-
Mold Design
-
Mold Manufacture
-
Mold Repair/Modification
-
RIM Molding
-
Precision Painting
-
Silk Screening
-
Assembly