Case Study
JBT Corporation
Replacing Sheet Metal
Reaction Injection Molding of plastic parts is a quality driven, price alternative compared to many manufacturing processes including sheet metal. With RIM, one can develop a sculpted, structural design that minimizes hardware and includes value-adding features, all at a price point that is cost-effective for low to mid-range volumes, especially for larger complicated parts. JBT Corporation, the world’s largest supplier of Automated Guided Vehicle (AGV) Systems, turned to Exothermic Molding for the tooling and manufacturing of two key housing parts, compartment covers that would afford them both the value, look and finish found in RIM.
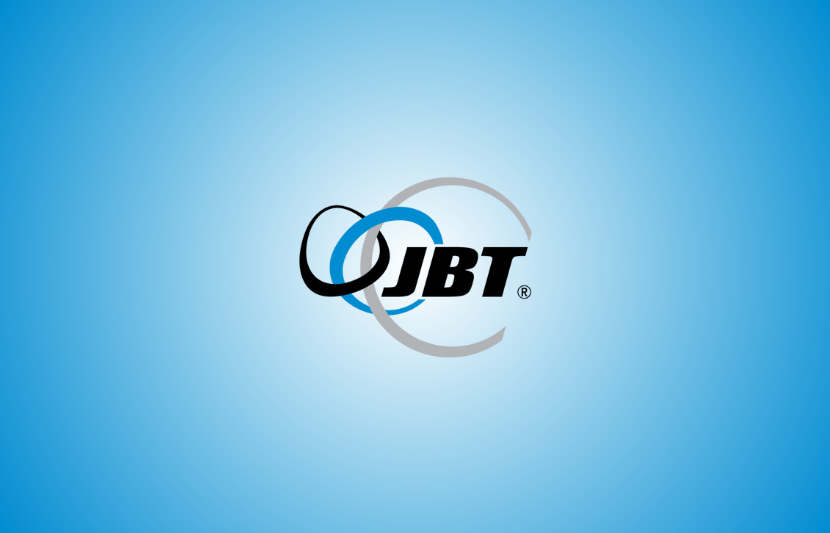
JBT Corporation is a leading global supplier of Automated Guided Vehicle (AGV) Systems. With over 125 years of experience in materials handling and 25 years’ experience in AGVs, JBT has the corporate strength and experience to make each AGV system a success. As a key supplier of AGV Systems since 1985, JBT Corporation has delivered over 400 AGV systems including 3,500 AGVs
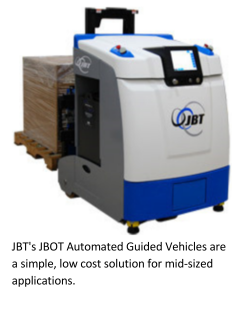
Guided Vehicle (AGV) Systems by JBT provide automated material movement for customers in a wide variety of industries including the automotive, chemicals/plastics, hospital, printing, FMCG (Fast Moving Consumer Goods), food & beverage, pharmaceutical, warehousing & distribution, and manufacturing industries.
When developing the latest counterbalance AGV design, JBT wanted to maximize the value delivered to its customers. It turned to Insync Design to assist with the form and structure of its AGV. Insync outlined the strengths and weaknesses of multiple fabrication JBT's JBOT Automated Guided Vehicles are a simple, low-cost solution for mid-sized technologies and RIM was chosen for the upper and front covers because of specific benefits that added value to the design and durability of the AGV housing:
Insync Design Corporation used the RIM Plastic process in the Industrial Design of JBT’s new AGV, because of its durability (in a sometimes-hostile environment of material handling), parts consolidation, and the ability to give the overall appearance of the machine a clean contemporary ID, while achieving design lines not achievable, in the old plate and weld process (of sheet metal).
Stephen Miggels – President
Insync Design Corp
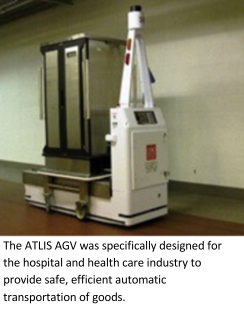
Insync referred JBT to Exothermic Molding for manufacturing the high-grade RIM molded plastic covers as an alternative to sheet metal. Two plastic RIM covers replaced a large metal cover that was used on the previous design. These plastic covers were an excellent solution for JBT because the modern styling matches the advanced robotic hardware and software technology used on the AGVs. In addition, the cost per piece of the plastic covers was significantly less than the complex, large metal fabricated cover.
At first glance, sheet metal looks to be a very low cost option for part production and modification, but this process sacrifices many design features and often adds to part cost. RIM allows for much more intricate and sophisticated design geometries compared to sheet metal. Engineers enjoy much greater design freedom to create attractive, sculpted parts. Features on the inner or outer surface of a sheet metal part must be cut out, welded, or bolted on as a secondary process. With RIM these features are molded into the part, reducing assembly, adding value to the overall design, and ultimately lowering unit costs.
An additional benefit worth noting is that materials cannot be encapsulated in sheet metal. Only RIM can encapsulate glass, metal, wood, wiring, circuit boards, and other parts for optimum protection and strength.
Both processes are capable of an excellent finish, however Exothermic Molding takes RIM part finishing to a higher level with superior quality clear-coat “automotive grade” finishes, advanced paint texturing techniques, and multi-color silk screening for improved branding. Sheet Metal can be costlier to paint, as labor time associated with special masking and treatment of joints exceeds that associated with RIM.
As JBT discovered, the cost of RIM produced parts for their AGV’s is significantly less costly than the large metal fabricated cover. Sheet metal might be a cost-effective option for small production volumes, but RIM should be taken into consideration if the part design is complex or if there is a longterm product life. RIM molding can incorporate features, such as structural stiffeners and mounting The ATLIS AGV was specifically designed for the hospital and health care industry to provide safe, efficient automatic transportation of goods. hardware, directly into the mold and the result is less secondary part assembly. Also, and important for the AGV application, RIM plastic parts serve as an enhanced sound and vibration insulator when compared to sheet metal. The parts are generally lighter weight and highly corrosion resistant.
JBT continues to test the bounds of imagination with designs that improve a full array of ruggedly built AGV types to meet their customer’s toughest material handling challenges. The RIM covers have already been incorporated into the latest Tug type AGV design and the covers will be incorporated into future standard vehicle designs. Exothermic Molding is prepared to meet these rigorous current and future design requirements and deliver vehicle parts that reduce material costs while standing the test of imagination and durability.
The benefits of reaction injection molding include:
-
Large, sculpted parts can be molded economically.
-
Variable thickness walls within the same mold allow for greater design freedom.
-
Wall thickness may range from .125 to 1.125 inches.
-
Closed molds produce accurately molded and structurally strong parts.
- Lower tooling cost and shorter tooling lead time.
-
A wide variety of material properties including UL94VO.
-
Electronic components, metal parts, glass and other materials are easily encapsulated.
-
RIM parts are lower cost than the same parts made from metal or fiberglass.
-
Compared to fiberglass, RIM parts have improved repeatability.
-
Composites - RIM parts can be reinforced with many materials.
Exothermic Molding capabilities:
-
CAD Engineering Review
-
Mold Design
-
Mold Manufacture
-
Mold Repair/ Modification
-
RIM Molding
-
Precision Painting
-
Silk Screening
-
Assembly