Case Study
Gatan
Cost Savings & Improved Quality
The need for change was apparent. Cast Urethane was no longer the process of choice.
Gatan, Inc. took a very hard look, and applied a very sharp pencil, when analyzing the cost of producing parts in Cast Urethane. The decision to use Reaction Injection Molding was simple. The RIM Process
provided important values: unlimited mold life, higher tolerance, more robust parts, and significantly lower cost. when the time came to shift production of the company’s premier parts to the new process, research lead Gatan to Kenilworth, New Jersey, and the expertise of one of the country’s leading RIM manufacturers of first-class plastic instrument housings.
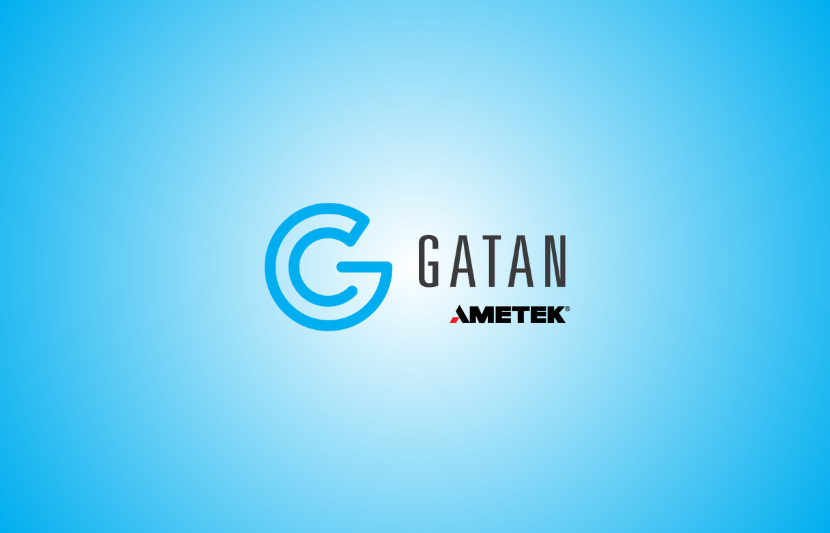
…we were using a soft mold (silicone rubber) to make these parts, and we were getting about 24-25 covers per run before we had to redo the mold, so it was costing us an absolute fortune, because every 25 covers, we would have to spend $4,000 more on another soft mold, then run 25 more covers, then spend $4,000 more. It was just costing us a fortune…[i]
John Duffy
Materials Manager SP&H, Supply Chain
Gatan, Inc.
Duffy knew the change from Cast Urethane to RIM was imminent, and he was determined to find the right solution with the right manufacturer. His associate, Dr. Steve Coyle, had initially favored Reaction Injection Molding as the preferred process over others, so when the decision was made to migrate production to RIM, John Duffy found himself at the Greater Pittsburgh – Design to Part Tradeshow.
“…a bunch of us went to a trade show (featuring) different kinds of molding technology, and one of the things we were looking for was RIM. And, I actually had the drawings in my hand, and I was walking up and down the aisles yelling “does anybody do RIM molding here?” recalls Duffy. “And, nobody there did RIM.”
He continues on, “Except a gentleman walked up to us. It was Ian White, President of DesignDesign Inc. in Kennett Square, Pennsylvania. Ian walked up to me and said, ‘I do not do RIM molding, but I design for RIM molding, and I work with a manufacturer that does the actual molding. I think I can help you.’” That discussion with Ian White precipitated an introduction to Exothermic Molding, and the relocation of cabinet production for the Gatan PIPS II ion polishing and PECS II broad argon ion beam systems.
Gatan, Inc. is a member of the Medical and Scientific Imaging segment of Roper Technologies, an S&P 500 and Fortune 1000 company. Roper designs and develops
software (both software-as-a-service and licensed), and engineered products and solutions for healthcare, transportation,
food, energy, water, education and academic research markets worldwide.
As part of an array of highly sophisticated, specialized tools, Gatan produces the premiere PIPS II and PECS II systems used in research laboratory specimen preparation. The PIPS II is a precision ion polishing system for exact centering, control, and reproducibility in the milling process. Argon beams are collimated (rays of light running in parallel) allowing for damage-free preparation of specimens in the material sciences (metals and alloys, highly sensitive chemicals, composition analysis, and the complexities of semiconductor materials and devices). Electron Microscopy Group in Nano-Materials Research Institute of AIS.
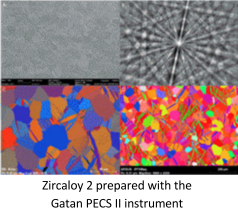
The PECS II system is a fully automated argon ion polishing system used for preparation of SEM (scanning electron microscope) samples to prepare damage free surfaces, cross sections and deposit coatings to protect or eliminate charging. The Ringe Group ofRice University is an example of how the technology is practiced. The tool is used in the structural and cellular biological studies of living specimens, drug discovery, and other medical research.
Additionally, both the PIPS II and PECS II systems are used for specimen preparation and analysis in the Oil, Gas and Geosciences, as well as Energy (battery, solar and LED), Utilities and Environmental Sciences.
Gatan products are considered preeminent tools by researchers. “…the view of customers is that they are quite loyal to Gatan. They look at us as a premiere provider of instrumentation for basic research, and I would say the people we are dealing with are really kind of leading edge. Some of these people (researchers) end up on the cover of science or nature publications where they found, for instance, a new way to
construct a polymer, or (made a) life science discovery.
They really look at us as a tool that can enhance their existing electron microscope, and make the performance even higher. (They) look at it from the perspective that it’s very much cutting edge…they expect high end performance from us.”
Jennifer McKie – Vice President, Global Marketing
Gatan, Inc
John Duffy adds, “You know, quality is very important to us. We consider ourselves the Cadillac in the industry. We want a product that functions with the best. We want a product that looks the best.”
Reaction Injection Molding brought to bear aspects of manufacturing the parts that were not sustainable with Cast Urethane and Rubber Molds. Quality, repeatability, and the capacity to accommodate intricate design are foremost with RIM at Exothermic.
When considering the look of the PIPS and PECS parts, there is an elegance in the design – the sweep as one moves from front to rear, the slight bevel that leads to the touch screen, the stack at the top with slender recesses that travel along the side. The part was designed in such a way that cosmetics would not be compromised by a robust system of fasteners.
There’s just enough in the design to make it elegant without making it overthought or over designed. “It’s more of a form and function type of piece with clean aesthetics,” adds Jennifer McKie.
Maintaining the repeatability of a design, whether simple or highly complex, is easily achievable with reaction injection molding. Cast urethane falls short in accommodation. John notes that the rubber mold process has an inherent recurrence deficiency beyond the cost issues: “…as they mold with a silicon mold, each time a part (is removed) the mold degrades, so there is a difference between part number one and part number twenty-four. Where part number twenty-four (does not maintain) quite the same tolerances, and look and feel, as part number one. So, yes that is a big problem with soft molding. The RIM parts are right on all of the time.”
Beyond the recurrence is the strength factor. RIM parts are typically stronger and more accurate. Resistance to temperature variation and maintaining structural integrity are both inherent advantages with the process.
Dr. Steve Coyle, Engineering Manager, Specimen Preparation Group at Gatan, shares his experience: “I think the bigger problem we actually were having was temperature related. These (housings) were being made in Phoenix and shipped to us, and when it was hot, they would just warp horribly. In my mind that was the biggest reason we had to get away from (cast) urethane, it’s just that it wouldn’t hold its shape.”
John Duffy notes that there was additional cost in transport as well, “We actually had to come up with special packaging…to hold them rigid, because if there was any space in that packaging, they would slump, and spread out…it didn’t quite work as well as hoped.”
Dr. Coyle adds, “I still have one in my lab somewhere, that more or less melted (in transport) …it’s actually pretty humorous.”
The aluminum molds created at Exothermic Molding accommodate variable wall thicknesses, yield strong and accurate parts, and enjoy life cycles that well exceed rubber molds. The life cycle of an aluminum mold could last thousands of cycles and well beyond ten years as compared to silicon rubber molds that typically last for 25 cycles. Using rubber molds for long-term production is very expensive compared to RIM Molding. Machined aluminum RIM molds simply don’t wear out and end up saving in the long run.
Aluminum RIM molds are also flexible for part adjustments. Mold changes to part configuration is easy to do. Making a financial commitment to a mold, then having a part change and discarding the existing mold for a new one, is a concern that is alleviated for both the designer and OEM. Given the multiple benefits: the life of aluminum molds versus rubber molds, the design flexibility of RIM (accommodating complex geometry), high repeatability, strength, accuracy, superior quality, John Duffy was asked if Gatan would ever go back to Cast Urethane: “…absolutely not… (and) we’re saving a ton of money using RIM.”
—————————–
[i] TELCO interview: Exothermic Molding, Kenilworth, New Jersey and Gatan, Inc., Pleasanton, California. Friday, October 23, 2015 10:00 AM11:00 AM (UTC-08:00) Pacific Time (US & Canada). Gatan, Inc., Steve Coyle: Engineering Manager, R&D, John Duffy Materials Manager SP&H, Supply Chain, Thijs Hosman: Project Manager, Specimen Prep, Jennifer McKie: Vice President, Global Marketing, and Scott Shiring:
Manufacturing/Process Engineer Mechanical. Interview by Joseph R. Passarella, Exothermic Molding, Inc.
[ii] Photos courtesy of Gatan, Inc. website, resources, media library. www.gatan.com