Case Study
Solidscape
Evolution into RIM Casements
The Reaction Injection Molding of plastic parts exceeds Industrial Design and mechanical engineering expectations as a quality-driven, price alternative to many manufacturing processes -- the most noteworthy of those methods being Thermoforming.
Mark Magee, Senior Design Engineer of the visionary 3D printing equipment manufacturer, Solidscape, Inc., a Stratasys company, says RIM has become the “go-to” process when Solidscape manufactures its industry-leading printers.
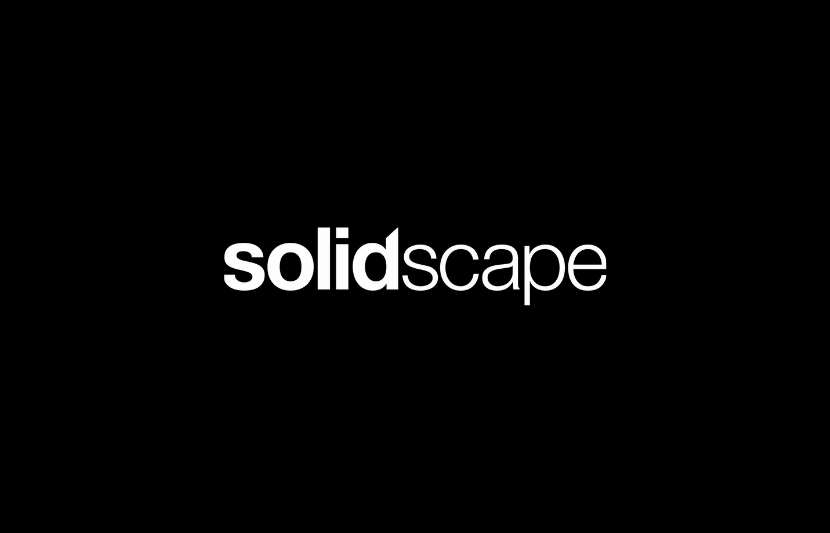
Company Overview
Solidscape®, Inc., a Stratasys company, is one of the largest, most innovative 3D printing companies globally with more than 4,000 high-precision 3D printers operating in over 80 countries for the direct manufacturing of solid objects designed in CAD.
To the credit of its founder, management, designers, and engineers, the company devotes itself to being at the forefront of this arena with very progressive technology and the highest standards.
The enlightened vision that is the fabric of the company’s core resonates not only in the future of 3D printing applications, but in the planning and manufacturing of its own product lines. Solidscape Design Engineers spare no effort in driving design ingenuity. Every possible process enhancement is explored to ensure the quality manufacturing of Solidscape products.
As Solidscape 3D printers evolved, housing production migrated from sheet metal to plastic in many of the configurations. Starting with the T66BT2 and T612BT2 series printers, and now the current EZ Print machines, Reaction Injection Molding of the casing is a key element of the manufacturing process.
"Solidscape, a Stratasys company, believes in innovation and offers more models and choices for a bigger range of possibilities — not just design-to-market rapid development, but a way to personalize and customize design."
Dan McCarthy, Vice President of Operations, Solidscape Inc.
“The RIM process is something that every young Design Engineer should learn about… it’s a process (where) tooling is very inexpensive. The part cost is reasonable. The part quality is excellent. The reliability is excellent. The durability is excellent… and, at a cost that is much less (than) that of injection and structural foam.”
Mark Magee, Senior Design Engineer, Solidscape Inc.
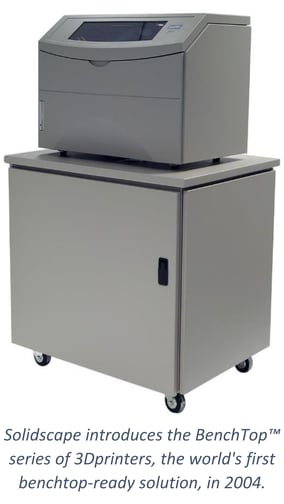
Design Process Alternatives
“Our design process has examined a number of alternative processes. We started out with metal, which was expensive (and) time-consuming. We went to a mixture of metal and thermoforming, which was a little bit better. It made the product look a little bit more ergonomic, but you still are very limited in the type of shapes and types of forms that you can get. So, we went to RIM which allows you the freedom to design much better shapes…and for structure is much better… we continually use RIM now…,” states Magee.
Characteristics of RIM Molding
Bayer AG, the developer of polyurethane, Reaction Injection Molding (RIM) technology, highlights the vivid progression of the technology as more and more product designers and manufacturers have discovered the unique capabilities and benefits of RIM for an ever-growing range of products. Comparable to thermoplastic injection molding, RIM is a plastics manufacturing process that uses precision-machined molds to create parts. The universal physical characteristics of polyurethane RIM parts are high strength and low weight. Depending on how the polyurethane RIM system is formulated, the parts can be foam or a solid, and they can vary from flexible to extremely rigid. Thus, polyurethane RIM processing can produce virtually anything from a very flexible foam-core part to a rigid solid part with widely varying densities and a range of specific gravities.
When asked why designers and engineers use other processes such as thermoforming, Mark Magee suggested that they use thermoforming due to a lack of awareness about the RIM process and its multitude of benefits. He describes it as a “general absence of familiarity with the benefits of RIM as a functional process.” The RIM process affords all the design freedoms that both injection and structural foam afford – the ability to accommodate bosses in the design, structure the part with molded-in ribs, and add in-mold or after-process metal inserts. In the end, these elements all lead to a much more robust finished part.
RIM Design Advantages
RIM is often a great alternative for designers who want the mainstream look of molded parts but cannot justify the tooling costs and volumes of typical thermoplastic parts. With RIM, one can develop a sculpted, structural design that minimizes hardware and includes value-adding features, all at a price point that is cost-effective for low to mid-range volumes, especially for larger complicated parts. Equally important benefits include:
-
Durability: Urethane RIM parts are highly durable, skid-resistant, mar-resistant, and virtually unbreakable.
-
Encapsulation: The low molding pressures and temperatures of RIM allow even the most sensitive electronic boards and components to be encapsulated without damage.
-
Appearance: The surface finish of RIM molded parts can be painted to produce Class A parts -- silk screening and other surface treatments can also be applied to add to the appearance and branding of the product’s design.
-
Reduced risk: The low-cost tooling investment of RIM alleviates risk while expediting lead times.
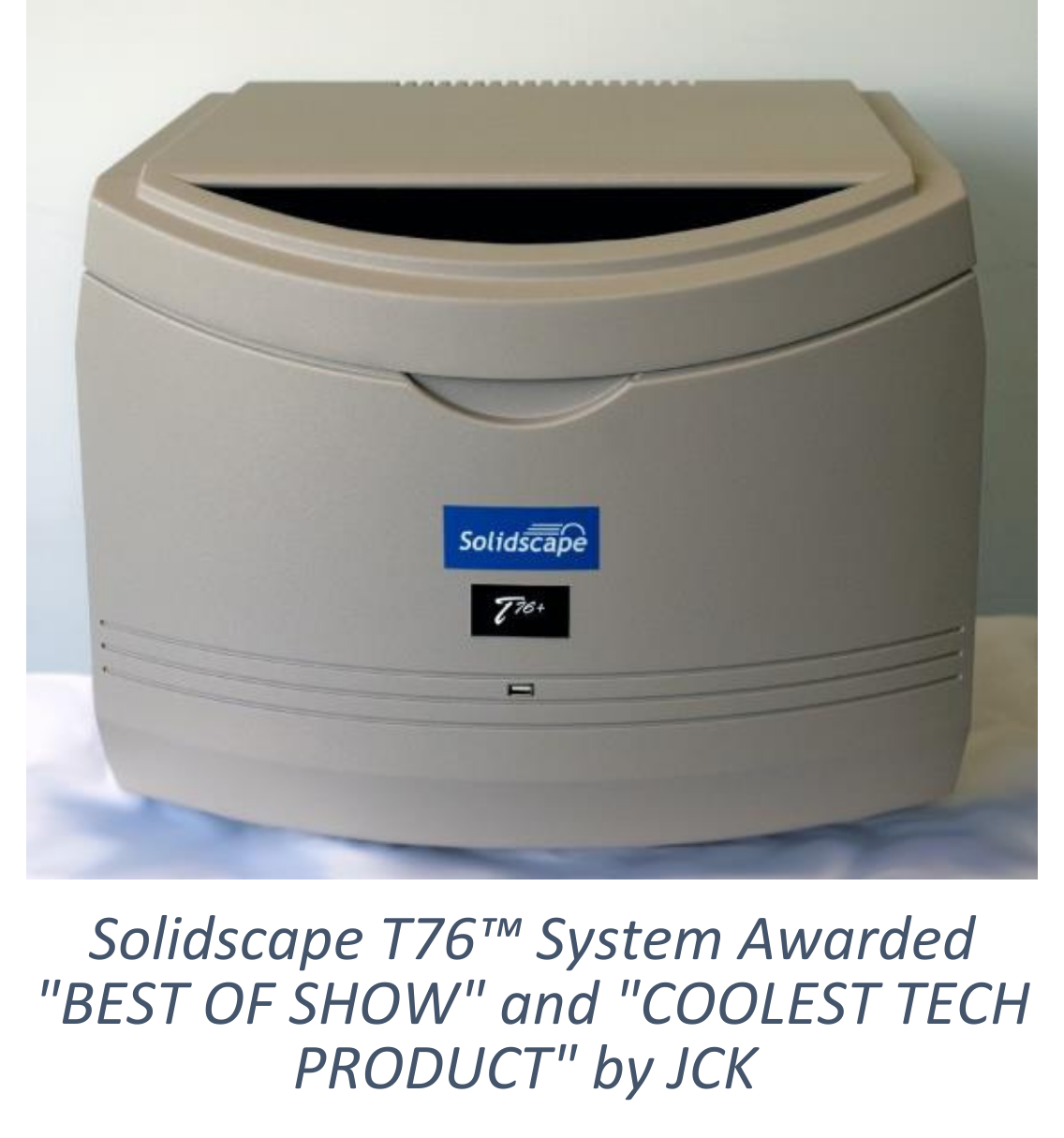
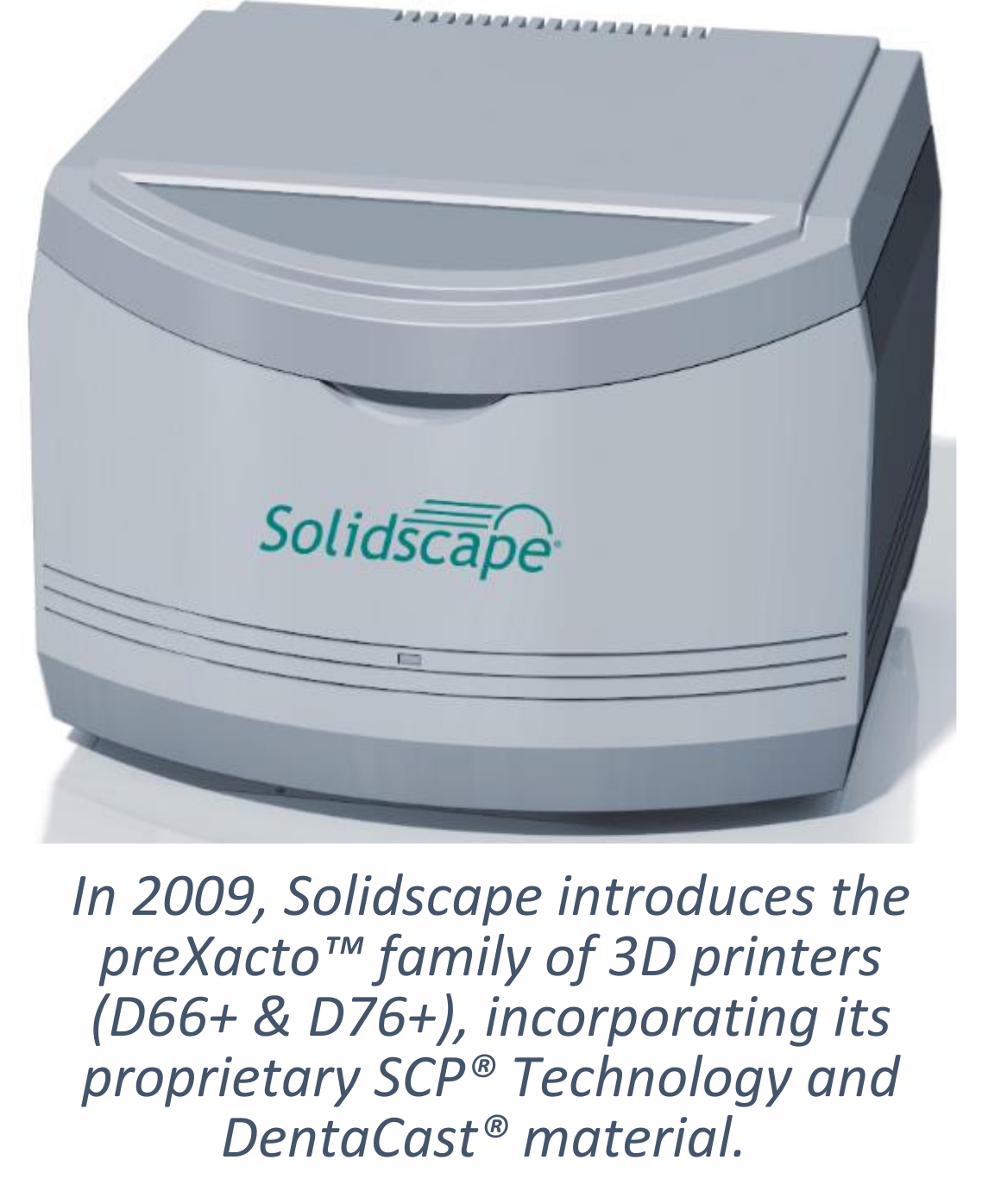
Magee concurs, “I did some research on RIM prior to using it… the part that interested me the most is that what I was expecting to receive for the cost was significant. And, I was pleasantly surprised that the cost of RIM could compare to thermoforming and (I would) receive much better and much cleaner looking parts. Appearance, structure, quality, durability, repeatability… the process is one that delivers what injection molding may deliver, but at a much less tooling dollar, probably in the vicinity of one-quarter the cost of the tooling in injection molding.”
He goes on to explain that the all-important consistency in part quality, the repeatability, is outstanding with RIM parts: “The variances part to part are very minimal. Once the process has been delivered for any given tool…the repeatability of that part from one to the next, from one cycle done this month to another cycle molded the next month, the repeatability is very tight. So, I understand that the lot that I receive today, and the lot I receive a month from now, two months from now, six months from now, they will all fit and interface with the other and the remainder of the parts similarly.”
When asked if he has experienced, or anticipates, any drawbacks in working with a process like RIM, he responds, “I don’t see any drawback in using the RIM process. You can understand what you’re going to receive, and consistently you receive the same product.”
Process Comparisons
Comparing RIM to other processes, the distinct advantages are clear. RIM outperforms competitive processes by providing benefits in all of the top sixteen most important areas of consideration.
Summary
Magee says, “The interesting part about going to RIM …was management’s expectations. It exceeded their expectation of what they wanted this machine to look like. It was a tough sell to spend the tooling money (on) a process that they did not understand. And, yet, now … it is the first process we look to go to for new design. We always weigh each and every type of process that is available to us in the volumes that we are doing, and RIM wins every single time. So, my expectations are always met with RIM.”
In the end, Magee notes that RIM meets every one of Solidscape’s most discriminating criteria, including the expectations of a visionary manufacturer.